Understanding Inconel 625: The Superior Nickel-Chromium Alloy
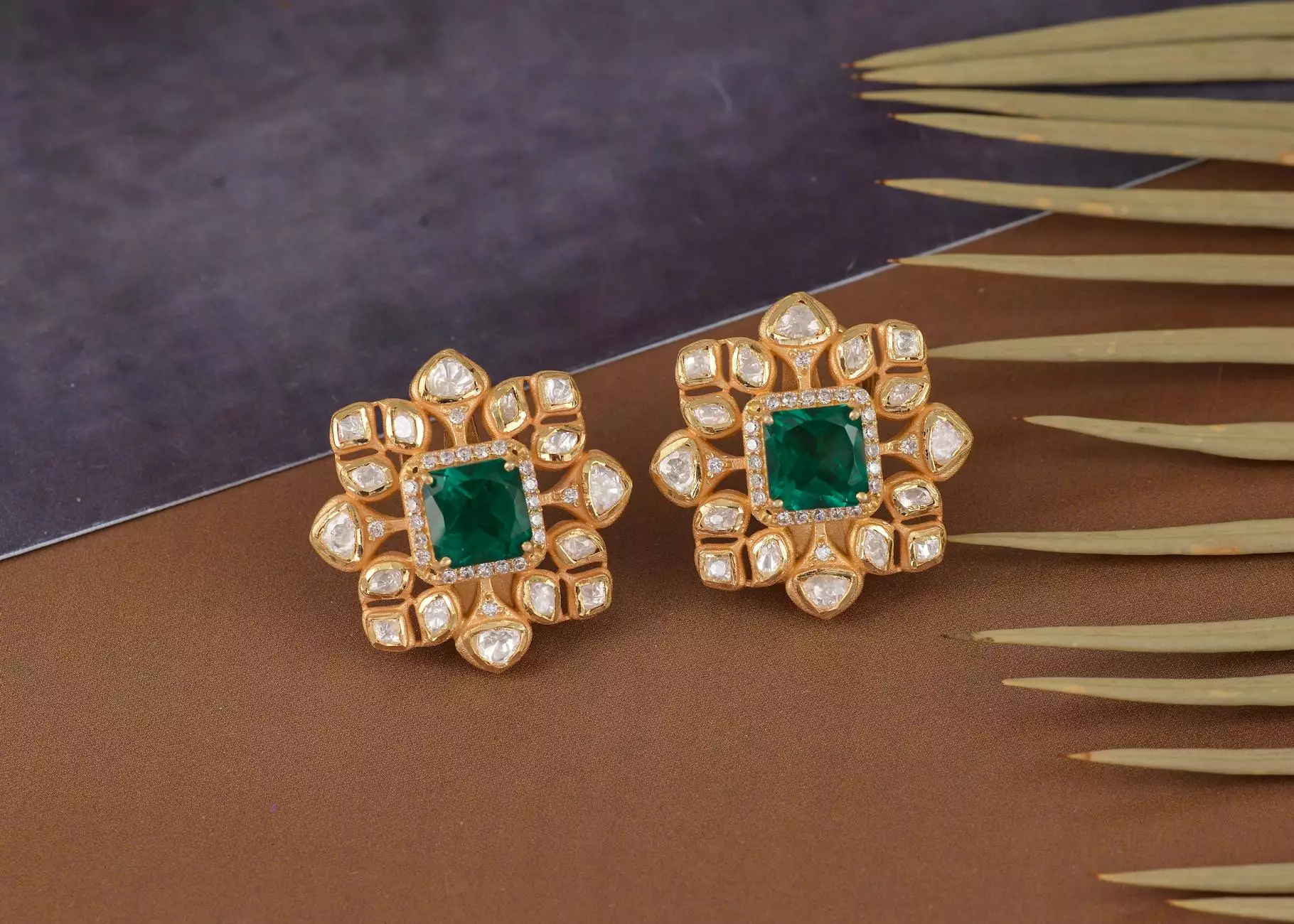
Inconel 625 is a remarkable nickel-chromium alloy that boasts superior strength, corrosion resistance, and weldability. This alloy is widely regarded for its ability to perform in extreme environments, making it the material of choice in numerous industries, from aerospace to marine applications. In this comprehensive article, we will explore the origins, properties, applications, and manufacturing processes related to Inconel 625, elucidating why it stands out among other materials.
What is Inconel 625?
Inconel 625 is a high-performance alloy primarily composed of nickel (58%), chromium (20%), and molybdenum (8%). The unique composition of this alloy provides exceptional resistance to oxidation and corrosion, along with the ability to withstand temperatures up to 2000°F (1093°C). The combination of these elements makes Inconel 625 particularly useful in challenging environments.
Key Properties of Inconel 625
Understanding the properties of Inconel 625 is essential for evaluating its applicability in various fields. Below are the key attributes that set this alloy apart:
- Corrosion Resistance: Inconel 625 exhibits remarkable resistance to pitting, stress corrosion cracking, and oxidation, making it suitable for harsh environments such as chemical processing and marine applications.
- High-Temperature Strength: The alloy maintains its mechanical strength even at elevated temperatures, making it ideal for applications in jet engines and nuclear reactors.
- Weldability: Inconel 625 can be easily welded and fabricated, which allows manufacturers to produce components with complex geometries without compromising structural integrity.
- Versatility: Its adaptability allows Inconel 625 to be used in various applications, from aerospace components to oil and gas pipelines.
Applications of Inconel 625
Given its outstanding properties, Inconel 625 finds applications across a multitude of industries. Below are some of the most significant sectors where this alloy plays a crucial role:
Aerospace Industry
In the aerospace sector, Inconel 625 is utilized in components subject to extreme temperatures and pressure. Components such as combustion chambers, gas turbine parts, and exhaust systems benefit greatly from the alloy's high-temperature strength and oxidation resistance.
Marine Applications
Due to its superior resistance to seawater and marine environments, Inconel 625 is extensively used in offshore oil rigs and marine engineering, including components like piping systems and pumps.
Chemical Processing
In chemical processing plants, where corrosive environments are commonplace, Inconel 625 serves as an excellent material for reactors, heat exchangers, and valves, ensuring longevity and reducing the risk of leaks or failures.
Oil and Gas Industry
The oil and gas sector relies on Inconel 625 for various applications, particularly in the production and transportation of oil and gas. Its durability in extreme conditions ensures that pipelines and all related components remain intact and functional.
The Manufacturing Process of Inconel 625
The manufacturing of Inconel 625 involves several nuanced steps to ensure the highest quality and performance of the alloy. Here’s a brief overview of the processes:
- Melting: The raw materials, including nickel, chromium, molybdenum, and small amounts of niobium, are melted together in a furnace to create molten Inconel 625.
- Alloying: During the melting process, specific proportions of the alloying elements are carefully monitored to achieve the desired material properties.
- Casting: The molten alloy is then cast into molds to shape it into semi-finished or finished products.
- Working: The alloy can be further processed by rolling, forging, or machining to produce finished components tailored to precise specifications.
Benefits of Using Inconel 625
The adoption of Inconel 625 in various sectors comes with a plethora of benefits that enhance product performance and longevity. Here are some of the key advantages:
- Longevity: Components made from Inconel 625 typically exhibit longer service life due to their resistance to wear and corrosion, which reduces the need for frequent replacements.
- Cost-Effective: While the initial cost may be higher compared to other materials, the extended lifespan and reduced maintenance costs render Inconel 625 a cost-effective option in the long run.
- Reliability: The combination of strength and resistance to environmental factors ensures that components perform reliably under load and stress.
- Sustainability: Utilizing Inconel 625 in applications promotes sustainability. The durability of the alloy contributes to less waste and more efficient resource use over time.
Inconel 625 in 3D Printing
3D printing technology has expanded the possibilities for producing complex geometries that were previously unattainable. Inconel 625 is an excellent candidate for 3D printing applications due to its remarkable strength-to-weight ratio and excellent thermal properties. Here's how Inconel 625 is reshaping the landscape of 3D printing:
- Complex Geometries: Inconel 625 can be printed with intricate designs that reduce material waste while enhancing performance.
- Customization: The flexibility of 3D printing allows for the easy customization of parts, catering to specific requirements in aircraft engines, medical devices, and more.
- Rapid Prototyping: Engineers can swiftly create prototypes using Inconel 625, allowing for quicker iteration and analysis of designs.
Conclusion
In summary, Inconel 625 is a versatile and high-performance nickel-chromium alloy that excels in applications where strength, corrosion resistance, and temperature stability are paramount. Its widespread use across industries such as aerospace, marine, chemical processing, and oil and gas speaks to its unrivaled capabilities.
As the demand for more durable and efficient materials continues to grow, Inconel 625 is set to play a crucial role in engineering innovations, particularly in the realms of product design and 3D printing. By understanding the properties and potential applications of this remarkable alloy, businesses can leverage its advantages to stay ahead in the competitive landscape.
Future Prospects of Inconel 625
Looking ahead, the potential for Inconel 625 continues to expand with advancements in technology and manufacturing processes. As industries demand materials that can withstand harsher conditions and deliver consistent performance, Inconel 625 is likely to remain a cornerstone material in many applications. Its integration into modern manufacturing techniques, including 3D printing, will further enhance its relevance in developing innovative solutions across various sectors.
For businesses interested in harnessing the benefits of Inconel 625, collaborating with specialized suppliers and manufacturers can facilitate access to high-quality materials tailored for specific applications. By investing in this robust alloy, companies can achieve greater efficiency and reliability in their products, ultimately contributing to their success in an ever-evolving market.