Understanding Electric Injection Molding: A New Era in Manufacturing
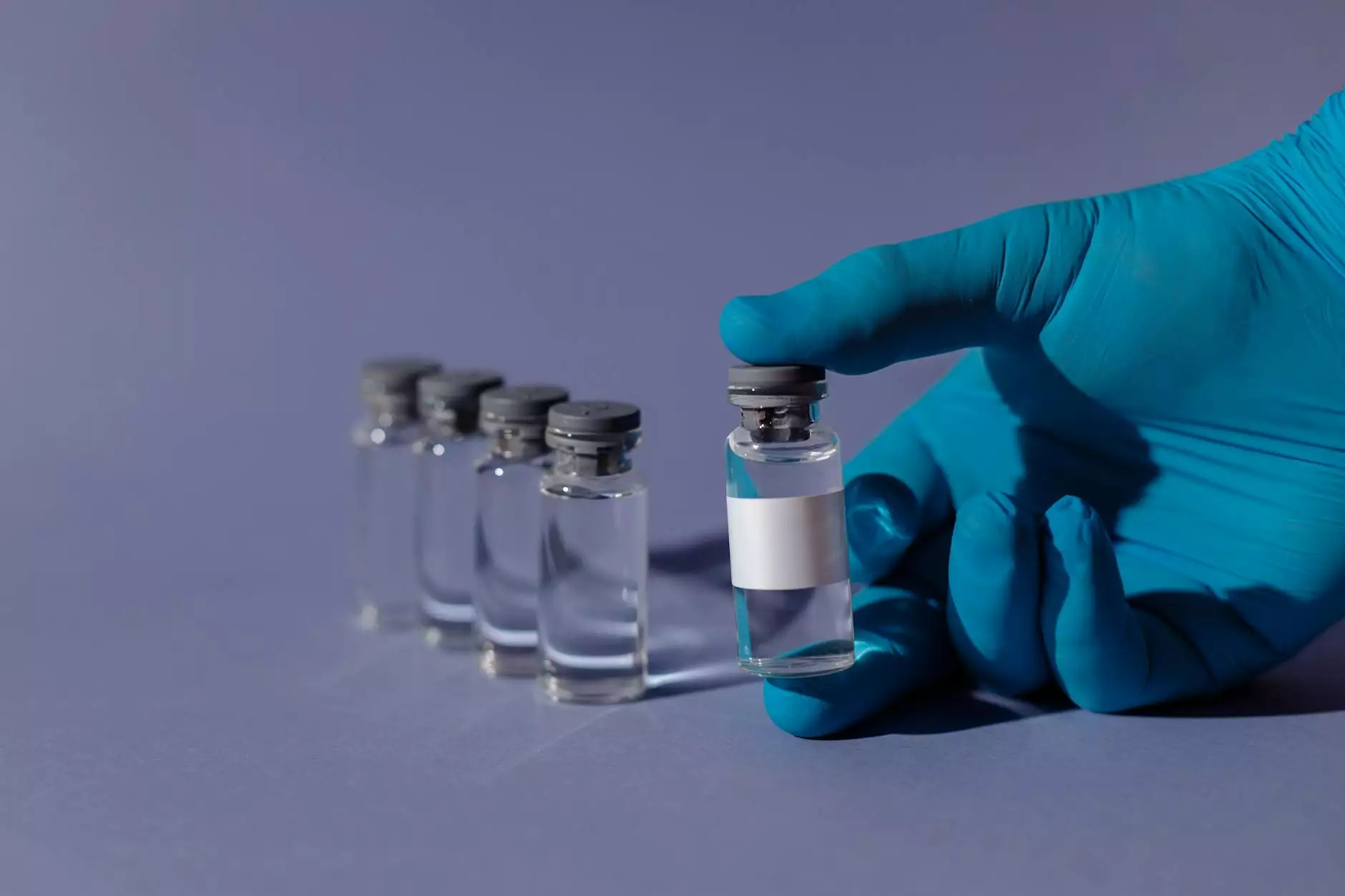
Electric injection molding is becoming an essential technology in the realm of manufacturing, especially among metal fabricators. This innovative process combines advanced machinery and computer technology to produce high-quality products with unparalleled efficiency. In this comprehensive guide, we will delve into the various facets of electrical injection molding, outlining its benefits, applications, and the reasons why it is a game-changer for industries across the board.
What is Electric Injection Molding?
Electric injection molding is a method of processing thermoplastic and elastomeric materials into various molded products. Unlike traditional hydraulic systems, which rely on hydraulic fluids, electric injection molding uses electrical drives, which results in greater energy efficiency, precision, and control.
The Mechanism of Electric Injection Molding
The core components of an electric injection molding machine include:
- Injection Unit: Responsible for melting the plastic and injecting it into the mold.
- Molding Machine: Supports the injection unit and houses the mold.
- Mold: The cavity that gives shape to the final product.
- Control System: Allows for precise adjustments and monitoring of the molding process.
Initially, pellets of plastic material are fed into the barrel of the injection unit. The electrical heating melts the plastic, while a screw mechanism and pressure ensure it's injected into the mold at a specific speed and temperature.
Key Advantages of Electric Injection Molding
The transition from hydraulic to electric systems offers numerous advantages that significantly benefit manufacturers and end-users alike. Here are some of the essential benefits:
1. Enhanced Energy Efficiency
Electric molding machines consume less energy compared to their hydraulic counterparts. They operate by employing servo motors that only draw power as needed:
- This efficiency leads to lower operating costs.
- Reduces the carbon footprint, aligning with sustainable manufacturing practices.
2. Greater Precision and Control
The precision of electric systems is significantly higher. The following aspects contribute to this advantage:
- Accurate Injection Speed: The ability to control the speed of injection minimizes defects.
- Consistent Temperature Control: Maintains a uniform temperature throughout the cycle, improving product quality.
- Less Variation: Reduces product variability, promoting consistency across batches.
3. Faster Cycle Times
With the rapid response of electric motors, manufacturers can achieve shorter cycle times, thus increasing productivity. This efficiency can lead to:
- Higher output rates.
- Quicker turnaround times for product delivery.
4. Reduced Maintenance Costs
Electric machines generally have fewer moving parts and eliminate the need for hydraulic fluids:
- This leads to less wear and tear and potentially lower maintenance costs.
- Also, reducing maintenance downtime enhances overall productivity.
5. Improved Workplace Safety
Electric injection molding machines produce less noise and eliminate the risks associated with hydraulic systems:
- They often include safety features such as automatic shut-off, enhancing operational safety.
- Reduced risk of hydraulic leaks ensures a safer working environment.
Applications of Electric Injection Molding in Metal Fabrication
Electric injection molding can be employed in a multitude of industries, particularly in metal fabrication. Some of the prominent applications include:
1. Consumer Products
Many household and personal items rely on electric molding, such as:
- Plastic containers
- Electronics casings
- Household appliances
2. Automotive Industry
In the automotive sector, electric injection molding is used to manufacture various components, including:
- Dashboard fittings
- Interior trim pieces
- Battery housings for electric vehicles
3. Medical Devices
The medical industry benefits greatly from this technology, producing:
- Surgical instruments
- Medical grade housings for devices
- Pharmaceutical packaging
4. Aerospace Components
Due to stringent safety and quality standards, the aerospace sector utilizes electric injection molding for:
- Lightweight components
- Complex shapes that require precision manufacturing
5. Industrial Equipment
Electric injection molding is used to create parts for industrial machines, ensuring that:
- Components can withstand rigorous industrial conditions.
- High performance and durability are achieved.
Future Trends in Electric Injection Molding
The advancement of electric injection molding technology is expected to continue transforming the manufacturing landscape. Some future trends include:
1. Adoption of Industry 4.0
With the rise of smart manufacturing, more companies are integrating IoT technology into electric injection molding processes:
- This allows for remote monitoring and real-time data analysis.
- Optimize machine performance and reduce downtime.
2. Increased Use of Recycled Materials
Sustainability is becoming a significant focus, and the use of recycled materials in electric molding processes is on the rise:
- This aligns with the global push for environmentally friendly manufacturing practices.
- Improves material circularity and reduces waste.
3. Continuous Innovation in Automation
Automation is key to enhancing efficiency and reducing human error. Advancements in robotics and machine learning will lead to:
- More sophisticated automated processes.
- Improved quality assurance throughout the molding cycle.
Conclusion
In summary, the transition to electric injection molding offers numerous advantages, including enhanced efficiency, precision, and sustainability. As the manufacturing industry continues to evolve, electric injection molding technologies will undoubtedly play a critical role in meeting the demands of modern production.
For metal fabricators and manufacturers, embracing this innovative technology is not just an option; it's becoming a necessity to remain competitive in a rapidly changing marketplace. At Deep Mould, we are dedicated to being at the forefront of this transformation, providing our clients with the highest quality products and services that leverage the latest in electric injection molding technology.
Contact Us
If you're interested in learning more about electric injection molding and how it can benefit your business, don't hesitate to reach out. Our team of experts at Deep Mould is here to assist you with all your metal fabrication needs.