Comprehensive Guide to Hydraulic Fitting Identification
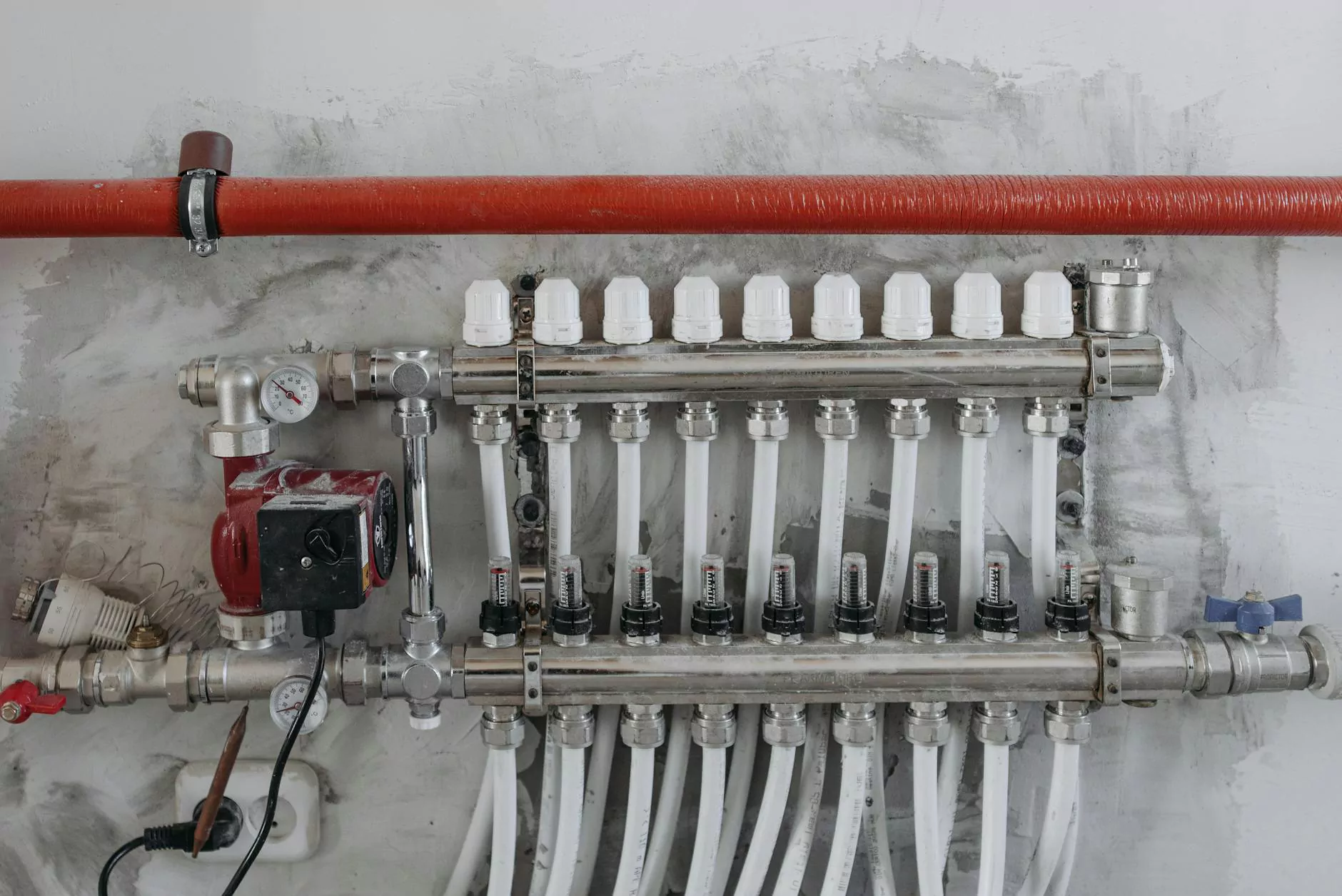
In today's industrial landscape, the importance of hydraulic systems cannot be overstated. These systems are essential for efficiently transmitting power and managing machinery operations across various sectors, from manufacturing to transportation. At the heart of these systems lies a vital yet often overlooked component: the hydraulic fitting. This article aims to provide an in-depth understanding of hydraulic fitting identification, crucial factors to consider, and practical insights that will help you ensure optimal functionality in your hydraulic applications.
What Are Hydraulic Fittings?
Hydraulic fittings are specialized connectors designed to join hoses, pipes, and tubes in hydraulic systems. These fittings serve several critical functions, including:
- Sealing: Preventing leaks by creating tight connections.
- Support: Providing structural integrity to hydraulic routes.
- Control: Allowing for the regulation of fluid flow and pressure within the system.
Understanding the correct hydraulic fitting identification is essential to ensure that your system operates efficiently and effectively. Incorrect fittings can lead to performance issues, leaks, or even catastrophic system failures.
Types of Hydraulic Fittings
Hydraulic fittings come in various types, each designed for specific applications and environments. Here is an overview of the most common types:
1. Threaded Fittings
Threaded fittings utilize a screw mechanism to create a secure connection. They come in both internal and external threads and can be made from different materials like steel, brass, and plastic. Key subtypes include:
- NPT (National Pipe Thread): Tapered threads that seal on the threads themselves.
- BSP (British Standard Pipe): Commonly used in Europe, available in parallel (BSPP) and tapered (BSPT).
- JIC (Joint Industry Council): Flared fittings with 37-degree angles for secure connections.
2. Flare Fittings
Flare fittings are designed to connect tubes at a specified angle, creating a stable and leak-proof joint. The most common angle for flare connections is 37 degrees, as seen in JIC fittings.
3. Compression Fittings
These fittings utilize a compressive force to connect tubes without the need for welding or threading. They're often used in applications where flexibility and ease of installation are paramount.
4. Quick Couplers
Ideal for frequent disconnecting and reconnecting, quick couplers allow for fast changes of hydraulic connections. They are particularly useful in applications involving mobile equipment and machinery.
5. Welded Fittings
Welded fittings are integral parts of hydraulic systems that require robust connections. They are often used in high-pressure environments to manage significant stress and loads.
Identifying Hydraulic Fittings
Correctly identifying hydraulic fittings is crucial for maintaining and repairing hydraulic systems. Here are some essential steps and elements to consider:
1. Check the Thread Standards
Understanding specific thread standards is one of the first steps in hydraulic fitting identification. Always note whether the fitting uses international standards like NPT, BSP, or JIC. Each standard has distinct features:
- NPT threads are tapered, providing a self-sealing capability.
- BSP threads are parallel and require additional sealing methods, such as using PTFE tape.
- JIC fittings are flared at a 37-degree angle, offering strong leak-proof connections.
2. Measure the Diameter
Measuring the outer diameter of the fitting is essential. Use calipers to get an accurate measurement, as this will help determine compatibility with hoses or tubes. It's crucial to measure both the male and female ends to ensure a proper fit.
3. Identify the Material
Hydraulic fittings come in various materials, including steel, stainless steel, brass, and plastic. Identifying the material can provide insights into the fitting's applications, durability, and resistance to environmental factors. For example:
- Steel fittings are generally strong and suitable for high pressure.
- Brass fittings are less corrosion-resistant but enjoy widespread use in various applications.
- Plastic fittings are lightweight and ideal for lower pressure applications.
4. Observe the Configuration
The configuration of a fitting plays a significant role in its function. Some fittings are designed for specific angles, such as elbows and tees. Understanding the configuration will help in proper identification and application.
Common Standards and Specifications
When it comes to hydraulic fittings, it's vital to be aware of various standards and specifications that dictate design, performance, and compatibility. This knowledge can guide you in hydraulic fitting identification:
1. ISO Standards
The International Organization for Standardization (ISO) has established numerous standards for hydraulic fittings to promote safety and compatibility across various systems. For example, ISO 4414 specifically addresses the use of hydraulic fluids in machinery. Familiarizing yourself with these standards can ensure that your fittings meet necessary safety and efficiency guidelines.
2. SAE Standards
The Society of Automotive Engineers (SAE) has developed numerous standards that are widely recognized in the industry, including SAE J514, which covers flare fittings. Understanding these standards can help you choose the right fittings based on application requirements.
3. DIN Standards
The Deutsches Institut für Normung (DIN) provides standards mainly used in Europe. These standards address the dimensions, design, and application of hydraulic fittings, ensuring that products meet industry requirements.
Best Practices for Hydraulic Fitting Identification
To maximize the efficiency and performance of your hydraulic systems, consider the following best practices for hydraulic fitting identification:
1. Consult Manufacturer Manuals
Always refer to the manufacturer’s manual for specific hydraulic components. These documents often contain valuable information about fitting sizes, thread types, and recommended maintenance practices.
2. Utilize Identification Tools
Consider investing in identification tools and software that can help you determine the fitting types and sizes needed for your applications. Many manufacturers offer resources that categorize fittings by application, material, and size.
3. Perform Regular Maintenance
Conduct regular inspections of hydraulic fittings and connections to ensure they remain in proper working order. Monitor for signs of wear and leaks, as addressing these issues early can prevent costly downtime.
4. Train Staff on Identification Techniques
Providing training sessions on hydraulic fitting identification can enhance the efficiency of your operations. Ensure that your team is knowledgeable about standards, measuring techniques, and common fitting types.
Conclusion
In conclusion, hydraulic fitting identification is a crucial aspect of maintaining and operating hydraulic systems effectively. By understanding the types of fittings available, their specifications, and best practices for identification, you can ensure that your hydraulic systems operate at peak performance. Remember, the right fittings do more than just connect components; they play an integral role in the safety and efficiency of your hydraulic systems. For those seeking high-quality fittings, explore the range available at fitsch.cn, your trusted source for fittings for sale.
By following the insights provided in this guide, you will be well-equipped to tackle any challenges related to hydraulic fitting identification, ensuring your systems remain operational and efficient for years to come.