The Advantages of Laser Welding Cleaning Machines for Metal Fabricators
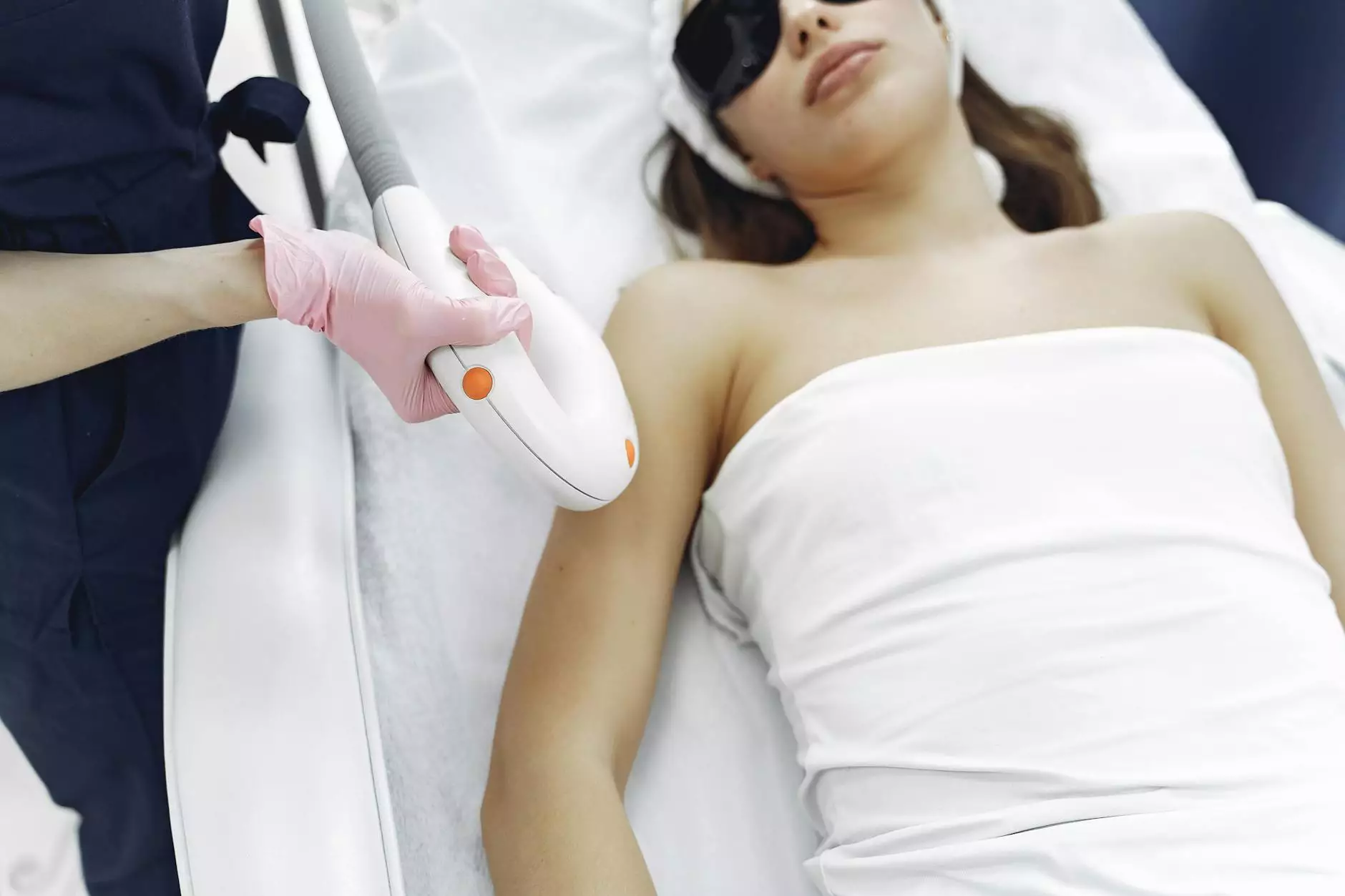
When it comes to cutting-edge technology in the metal fabrication industry, one tool stands out for its efficiency and effectiveness: the laser welding cleaning machine. In recent years, this innovative device has revolutionized the way metal fabricators work, providing a range of benefits that enhance productivity and streamline processes.
Enhanced Precision and Accuracy
One of the key advantages of utilizing a laser welding cleaning machine is the unparalleled precision and accuracy it offers. Unlike traditional cleaning methods, which may result in uneven surfaces and inconsistent welds, a laser machine ensures a uniform finish with minimal room for error. This precision is crucial in metal fabrication, where even the smallest imperfection can compromise the quality of the final product.
Improved Efficiency and Productivity
By investing in a laser welding cleaning machine, metal fabricators can significantly increase their efficiency and productivity. These machines are designed to perform cleaning tasks at a rapid pace, reducing downtime and allowing workers to focus on more critical aspects of the fabrication process. With faster cleaning cycles and minimal manual intervention required, businesses can complete projects in less time without sacrificing quality.
Cost Savings and Sustainability
Another compelling benefit of incorporating laser welding cleaning machines into metal fabrication operations is the potential for cost savings. These machines are known for their longevity and durability, requiring minimal maintenance and upkeep compared to traditional cleaning equipment. Additionally, the precise nature of laser cleaning reduces material waste, making it a more sustainable and environmentally-friendly option for businesses looking to minimize their carbon footprint.
Versatility and Adaptability
One of the standout features of laser welding cleaning machines is their versatility and adaptability to a wide range of materials and surfaces. Whether working with stainless steel, aluminum, or exotic alloys, these machines can effectively remove contaminants and prepare surfaces for welding with ease. This flexibility allows metal fabricators to tackle diverse projects without the need for multiple cleaning tools, saving both time and resources in the long run.
Enhanced Safety and Worker Well-Being
Ensuring the safety and well-being of workers is paramount in any industrial setting, and laser welding cleaning machines help achieve this goal. By minimizing exposure to hazardous chemicals and reducing physical strain associated with manual cleaning methods, these machines create a safer working environment for employees. This not only improves morale and job satisfaction but also reduces the risk of workplace injuries, ultimately benefitting both the workforce and the business as a whole.
Conclusion
In conclusion, the adoption of laser welding cleaning machines has proven to be a game-changer for metal fabricators seeking to optimize their operations and stay ahead of the competition. With benefits ranging from enhanced precision and efficiency to cost savings and worker well-being, these machines offer a comprehensive solution for businesses looking to elevate their fabrication processes. By investing in this cutting-edge technology, metal fabricators can position themselves for success in an ever-evolving industry landscape.